by
admin essence
| May 20, 2021
High strength and hardness, excellent thermal stability, good corrosion resistance and low density: this unique combination of properties makes silicon nitride (Si3N4) the ideal material for numerous industrial applications across diverse sectors such as automotive, electronics and biomedical. Research into Si3N4 began more than 60 years ago in conjunction with the development of internal combustion engines made entirely from ceramic. Thanks to modern manufacturing methods, this material can be processed in a highly flexible way, with excellent customisation capability to meet a wide range of requirements and potential applications.
Why choose Si3N4?
With excellent mechanical, thermal and physiochemical properties, Si3N4 is used in both traditional and highly innovative solutions. Its lightness, high flexural strength and wear resistance, as well as its ability to withstand the harshest environments, make Si3N4 a proven alternative – and sometimes the only alternative – to traditional materials such as stainless steel, tungsten carbide, oxide-based ceramics and silicon carbide.
These versatile ceramics offer enormous potential, much of which is yet to be exploited.
Examples of Si3N4 applications
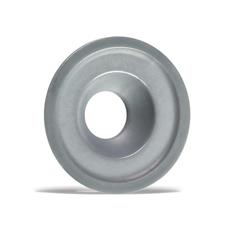 |
Slippers for axial piston pump |
Ceramics made with silicon nitride are used in numerous applications including ball bearings, metal cutting tools and automotive and aerospace components: diesel engines, turbocharger rotors, spark igniters, etc. Si3N4 is now also being used in even more innovative fields such as the electronics and biomedical sectors.
Thanks to its excellent biocompatibility, wear resistance and antibacterial properties, Si3N4 is indeed suitable for orthopaedic and implant uses.
Furthermore, its unique electrical properties, such as insulating capability and high dielectric rigidity, combined with its high thermal conductivity, thermal shock resistance and mechanical strength, make Si3N4 particularly suitable for electronic components.
Medical sectors
No hydrothermal ageing
|
Because it is not subject to hydrothermal ageing, silicon nitride is not altered when repeatedly sterilised in an autoclave. This makes it ideal for all types of medical instrument.
|
Grey colour
|
Silicon nitride is naturally grey in colour and does not require any additional colour treatment, making it ideal for the manufacture of components where white is not recommended.
|
High Weibull modulus
|
Statistically, mechanical strength remains stable across components manufactured in the same batch. The Weibull modulus of silicon nitride is higher than that of traditional ceramics, which makes it a safer candidate for medical applications.
|
Outstanding mechanical stability at high temperature
Low coefficient of thermal expansion (CTE)
|
Silicon nitride remains mechanically very stable at high temperatures. In addition, its coefficient of expansion (CTE) is extremely low; this means its dimensions remain unchanged across a very wide temperature range.
|
Handling fluids
Low coefficient of thermal expansion (CTE)
|
Dimensional aspects play a key role in this type of application, since expanding components can compromise the entire system.
|
High thermal conductivity
|
An important characteristic of silicon nitride is its high thermal conductivity, which facilitates the dissipation of heat generated by high friction or the transport of heated fluids.
|
Outstanding resistance to thermal shock
|
Relevant for applications in which ceramic components are subjected to significant temperature variations.
|
Watchmaking and jewellery
Grey colour
|
To avoid the plastic-like appearance of white coloured ceramics, the latter are usually treated with pigments when used in products with a high-perceived value; however this can compromise their mechanical properties. Silicon nitride, with its naturally grey or darker colour, is perfectly suited to the aesthetic and technical requirements of the watchmaking and jewellery sectors without additional pigmentation.
|
Low density
|
Whether for aesthetic or technical reasons, silicon nitride is an excellent choice for watch movements thanks to its low density. Lighter watch cases can be produced, which are more comfortable to wear. It also reduces inertia loss in movement components, which increases the duration of the power reserve.
|
High wear resistance
Low coefficient of friction
|
Silicon nitride's wear resistance significantly increases the service life of watch movement components. Its low friction coefficient improves movement operation both in terms of accuracy and power reserve.
|
Machinery and equipment industry
High wear resistance
|
Silicon nitride enables high-speed metal cutting thanks to its high wear resistance, which allow operations to be performed at speeds up to 25 times higher than those possible with traditional materials such as tungsten carbide.
|
High Weibull modulus
|
The use of a reliable material is vital in the field of cutting tools, particularly during long cycles.
|
Outstanding mechanical stability at high temperature
|
Its high strength and hardness, combined with its ability to withstand sudden temperature changes, give silicon nitride an edge over the ceramics traditionally used in cutting tools, such as alumina.
|
Low density
|
Silicon nitride usually has a density of 3.21 g/cm3 – 2.5 times less than that of steel and 1.4 times less than that of grade 5 titanium alloys.
|
EXPLOIT THE FULL POTENTIAL OF SI3N4 WITH CERAMARET
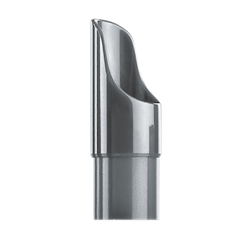 |
Tips for medical endoscopes |
There is no mistaking the potential of Si3N4. And yet, this ceramic still offers so many unexplored possibilities!
By joining forces with Ceramaret, you have the opportunity to take silicon nitride technology further, and apply all its benefits to your industrial applications. Ceramaret is a world leader in designing and polishing high-precision ceramic parts, and employs a very specific process for the treatment of Si3N4, which allows the material's properties to be exploited to the full.
The fruit of many years of research and development, this technology imposes no constraints in terms of geometry. It therefore makes it possible to manufacture extremely complex and very precise ceramic components.
Why choose Ceramaret?
Thanks to its technical expertise, Ceramaret is able to work with its customers to design high-precision ceramic parts and to help them choose the best material based on the desired properties. With involvement right from the design and development stages, Ceramaret is able to offer technically innovative and competitive solutions. Drawing on its cutting-edge in-house technical capability and expertise, Ceramaret designs superior tools and supports you throughout the entire manufacturing process.
For several decades, Ceramaret has been a world leader in the design and polishing of components made from the hardest materials. From engineering to stock management, Ceramaret is known for its ability to offer complete, customised solutions. Even on runs into the millions, each of our parts is manufactured with extreme precision and adapted for use in the most innovative applications.
The expertise of our staff and our state-of-the-art production sites offer significant benefits to our customers. Our ISO 9001:2015, ISO14001:2105, ISO45001:2018 and ISO13485:2016 certifications, combined with our quality policy, are your guarantee of success.
How do we produce Si3N4?
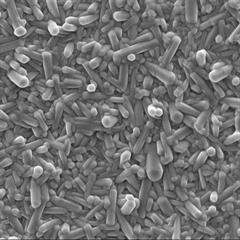 |
Typical needle-like microstructure of the silicon nitride beta phase |
Unlike previously developed silicon nitride components, which were obtained by creating a reaction between silicon powder and a nitrogen-rich atmosphere (Reaction Bonded Silicon Nitride [RBSN]), sintered silicon nitride requires the addition of sintering agents. The nature of the chemical bond between the silicon and nitrogen in Si3N4 powders makes densification of the material by heat treatment extremely difficult or even impossible. The strong covalent bond blocks the diffusion of the atoms, which is essential for sintering to occur. To make this possible, sintering agents such as alumina, yttrium oxide or silicon dioxide must be added. At the sintering temperature, these oxides lead to the formation of a liquid phase which, via capillary action, enables complete densification of the silicon nitride particles and the formation of a sintered monolith. Nowadays, different sintering techniques can be used to obtain fully dense silicon nitride components. Hot Pressed Silicon Nitride (HPSN), Hot Isostatically Pressed Silicon Nitride (HIPSN) and Gas Pressure Sintered Silicon Nitride (GPSN) are the most commonly used processes. Ceramaret uses Gas Pressure Sintering (GPS). This process is more efficient and reproducible than the other available processes, and the final material is of a higher quality. Because it does not impose geometric constraints, it fits well with the expertise and positioning of Ceramaret, which is traditionally known for its ability to produce complex and highly precise ceramic components.
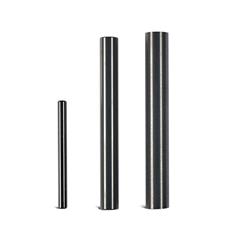 |
Shafts and plungers for motors and pumps with high precision and surface finish |
The application of pressurised nitrogen enables Si
3N
4 powder compacts to be sintered at higher temperatures, preventing thermal decomposition and facilitating high densification. However, the sintering parameters must be closely monitored to obtain high-quality solid monoliths. Finally, the higher sintering temperatures used in the GPS process enable the production of Si
3N
4 with a double microstructure, in which large elongated grains are dispersed within a matrix of fine grains. This microstructure offers superior mechanical properties. Following years of research and development, Ceramaret now employs a precision sintering process to produce high-quality components.
Ceramaret offers to its customers a wide range of products, which include components obtained using standard dry pressing as well as near net shape injection moulding methods. These methods enable industrial-scale production of simple or complex geometry components at competitive price and with an unprecedented level of customisation.
References:
G. Petzow, M. Herrmann, Silicon Nitride Ceramics, Structure and Bbonsding, vol. 102, Springer-Verlag Berlin Heidelberg 2002.
Robert B. Heimann, Classic and Advanced Ceramics: From Fundamentals to Applications, 2010 WILEY-VCH Verlag GmbH & Co. KGaA, Weinheim
Branko Matovic, Low Temperature Sintering Additives for Silicon Nitride, Dissertation an der Universität Stuttgart, Bericht Nr. 137 August 2003
Frank L. Riley, Silicon Nitride and Related Materials, J. Am. Ceram. Soc., 83 [2] 245–65 (2000)
Saurabh Lal et al., Biological Impact of Silicon Nitride for Orthopaedic Applications: Role of Particle Size, Surface Composition and Donor Variation, www.nature.com/scientificreports, 2018
Has this article convinced you of the advantages of silicon nitride? Would you like to find out how to use it to produce innovative and exceptional quality components? Contact our specialists for advice. We are involved right from the design phase and, thanks to our unrivalled technical experience, we can help you design robust, reliable and highly sophisticated parts from silicon nitride.
Contact us